When considering sustainable manufacturing practices, Pierce Manufacturing is leading the charge. As a manufacturer of some of the toughest and most customized fire apparatus in the world, Pierce’s business is much more than the products that come off the line each day and the innovative technologies that advance performance. Pierce’s manufacturing processes and remarkable business practices are the engines that empower people to progress towards a more sustainable future.
It takes a collaborative effort to move the needle with regard to protecting work environments and taking a green approach to manufacturing. At Pierce, our teams aim to lead the global shift towards new technology by working with customers, companies and across communities to make energy simpler, smarter and more sustainable.
Learn more about Pierce’s sustainability manufacturing practices and how daily operations continue to evolve to support environmentally focused initiatives.
Sustainable Manufacturing of Fire Trucks Includes:1. Following Fire Truck Manufacturing Environmental Guidelines
Environmental stewardship is crucial to achieving Pierce’s mission of driving positive change. Across the company, team members work in many ways to ensure that caring for people and the planet are at the forefront of how business is conducted. As one of Oshkosh Corporation’s leading brands, the organization’s Environmental Protection Policy and Energy Management Policy provide a consistent, enterprise-wide standard for minimizing the environmental impacts of operations.
2. Making Modifications to Fire Truck Manufacturing Facilities
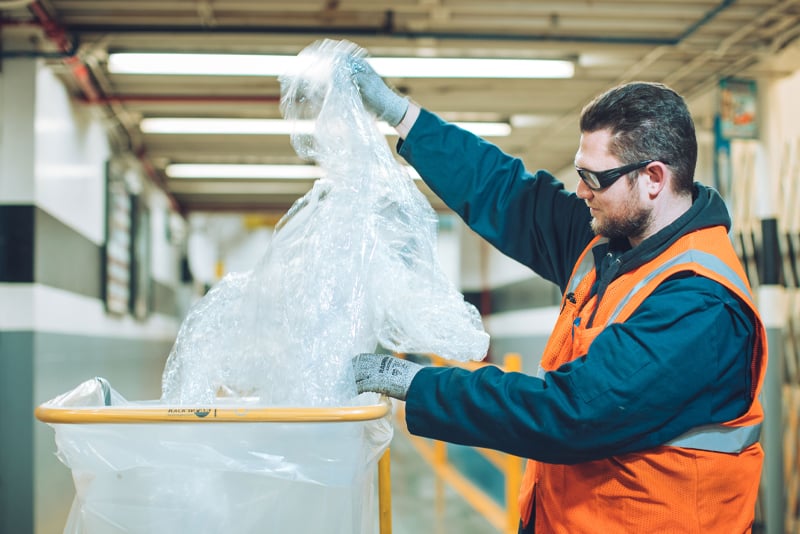
Pierce Facility Sustainability Enhancements Have Included:
- Converting operations and offices to LED lighting, increasing overall brightness and aesthetics of the manufacturing floor for our team members and customers alike, all while reducing associated maintenance and energy costs.
- Installation of motion sensors maximize the energy savings when people are not in the area.
- Creating a building management system that utilizes the data from the submetering of equipment and plant sections to identify trends and performance. Providing displays of the trending data to optimize real time information.
- Capturing waste heat from processes for alternative use.
- Designing a water boiler system that recirculates hot water with an on-demand system for area sinks and showers.
- Completing seasonal energy checklists.
- Increasing insulation throughout Pierce facilities to lower heating and cooling requirements.
- Building team member ownership to turn off equipment, including monitors and printers.
- Compressed Air Leak Surveys are completed to help identify where leaks are present, but not audible. Tool carts are stocked with the necessary tools to fix compressed air lines or quick release nozzles on the spot.
- Installation of variable frequency drives (VFDs) to various processes throughout the plants to reduce energy use. VFDs can reduce speed to 50% when the process stops for a predetermined time period.
- Modernizing HVAC and Air Makeup Units and adding these units to the building management system (BMS) dashboard to identify trends in energy usage.
3. Implementing Manufacturing Pollution Prevention Programs
Diverting waste from landfills is a key priority in all Pierce facilities. Within Pierce facilities, many materials are recycled, repurposed or replaced with recyclable materials.
Here are a few specific ways the reduce and reuse approach has been engrained throughout Pierce’s company culture.
- Standardization of refuse and recycling containers by color and labels.
- Standardizing provided consistency amongst all Pierce facilities. This standardization increased consumer recycling by over 400%.
- Pierce recycles the common materials; single stream consumer goods, including plastic bottles, aluminum cans, cardboard, paper and scrap metals.
- Plastic is recycled to be turned into benches. In the first year the team diverted 58 tons of plastic with 3 benches received so far.
- Reuse of product drums and shipping containers and tracking of all materials diverted from landfills.
- Since 2014, Pierce has sent over 100,000 pairs of used safety glasses to Contractivity, a Goodwill job training program to clean and repackage glasses.
- Post-consumer materials from the paint department are recycled and utilized for sustainable fuels which are then used to generate renewable energy.
- Wood pallets can be sent back to the supplier for reuse, internally reused or are sent to a pallet re-conditioner. Whatever cannot be reused is ground into landscape mulch.
- Electronic waste recycling events are held annually for team members. To date, 41,000 pounds of electronic waste for recycling has been generated.
- LED Lighting Fairs have been held through Focus on Energy and TechniArt to increase employee energy awareness. These fairs provided LEDs and other energy-saving items for team members at a reduced cost for personal use. Over 8,800 LEDs were purchased, saving employees over 10,600,000 kWh and $1M over the life of the bulbs––enough to power 1,267 homes for one year.
4. Incorporating Environmentally Friendly Materials and Features in Fire Truck Products
Pierce’s fire apparatus and technology development process starts by engaging with customers to understand and anticipate their needs. From material sourcing to manufacturing, to product transport and operation on the road, the Pierce product teams scrutinize every factor of a fire apparatus’ impact on the environment.
Explore Environmentally Friendly Materials and Unique Product Features of Pierce Fire Trucks:- Raw materials generated from scrap include aluminum and stainless steel, as well as aluminum from smelted ingot.
- Paint primers and topcoats are free of chrome and lead.
- Since 1994, significant reductions have been made to particulate matter and nitrogen oxide emissions.
- Pierce Idle Reduction Technology reduces the idle time of the main chassis engine, as well as reduced fuel consumption and service intervals over the life of the apparatus.
5. Maintaining Environmental and Sustainability Certifications and Practices
Sustainability goes beyond environmental responsibility. Pierce maintains a thoughtful focus on engaging people and communities, caring for the environment, developing innovative products and operating safely and responsibly. With the goal to improve every day and make a difference for customers, suppliers and the communities served, Pierce’s sustainable manufacturing practices are upheld by not only the performance metrics established, but the certifications held by the organization.
Pierce’s Environmental and Sustainability Certifications and Recognition Include:
- Certified ISO14001:2015 Environmental Management System (EMS) site – the first domestically for all of Oshkosh Corporation.
- The Green Master’s Program assessment and recognition program for Wisconsin businesses dedicated to improving sustainability initiatives. The program provides Pierce with a benchmark to compare sustainability performance with other companies in its sector.
- Recognized by Ethisphere as one of the World’s Most Ethical Companies.
- Recognized by RobecoSAM with the Industry Mover Award for critical steps taken to propel corporate sustainability by measuring impact and disclosing results.
- Recognized on the Dow Jones Sustainability Index (DJSI).
- As a result of Pierce’s commitment to green initiatives, the company was awarded the Focus on Energy 2020 Energy Efficiency Excellence Award.
- Pierce was awarded the Wisconsin Department of Natural Resources for Excellence in Recycling award.
-
Achieved TRUE (Total Resource Use and Efficiency) Zero Waste Certification at the Gold level. TRUE certification is administered by Green Business Certification Inc. (GBCI), an organization that independently recognizes excellence in green business industry performance and practice globally.
Pierce Employees Go Above and Beyond to Protect the Environment
The achievements made in product development, on the production floor and in the processes put into place throughout Pierce, extend far beyond the company’s walls and the fire apparatus in service. Pierce employees regularly show their dedication to the environment and the communities in which they live. Team members identify ways they can make an impact by recognizing ways their work influences our world.
For example, change from plastic bags to paper bags at the Pierce company store. Team members realized that it could take up to 1,000 years for a plastic bag to disintegrate in a landfill. By switching from plastic bags to 100% recycled paper bags, the store would not only save $2,000 per year but also expand the company’s sustainable practices at the store and wherever the bag ends up with our customers.
The Pierce team continues to make it a fundamental objective to reduce wastes and emissions to minimize adverse impacts on air, water and land. By preventing pollution at its source, team members can improve the quality of products and services, while maintaining a healthy and safe work environment while protecting the environment. You can see these initiatives across several locations.
The team in Bradenton, FL, sought out a sustainable method to increase their waste diversion from landfill. They were able to identify a process that takes end-of-use material and repurposes it into high energy, environmentally clean alternative fuel. From the beginning of this program to current, Pierce Bradenton has been able to increase their waste diversion over 12%.
The Segment Energy Team is a cross functional team that works to integrate the energy needs of the different sites and processes. The team works together to identify and categorize projects and confirm the best option.
In addition, the Fire & Emergency Material Flow Council utilizes Plan For Every Part best practices to improve environmental sustainability by instilling cross functional collaboration within the team and the external supply chain.
These efforts include:
- Reducing expendable packaging
- Engineering returnable packaging designs
- Reducing the Logistics carbon footprint
- Sourcing recycled materials
Would you like to work with a fire truck manufacturer that practices environmentally conscious processes? Talk to a Pierce representative or a dealer about how to achieve your sustainability goals.